
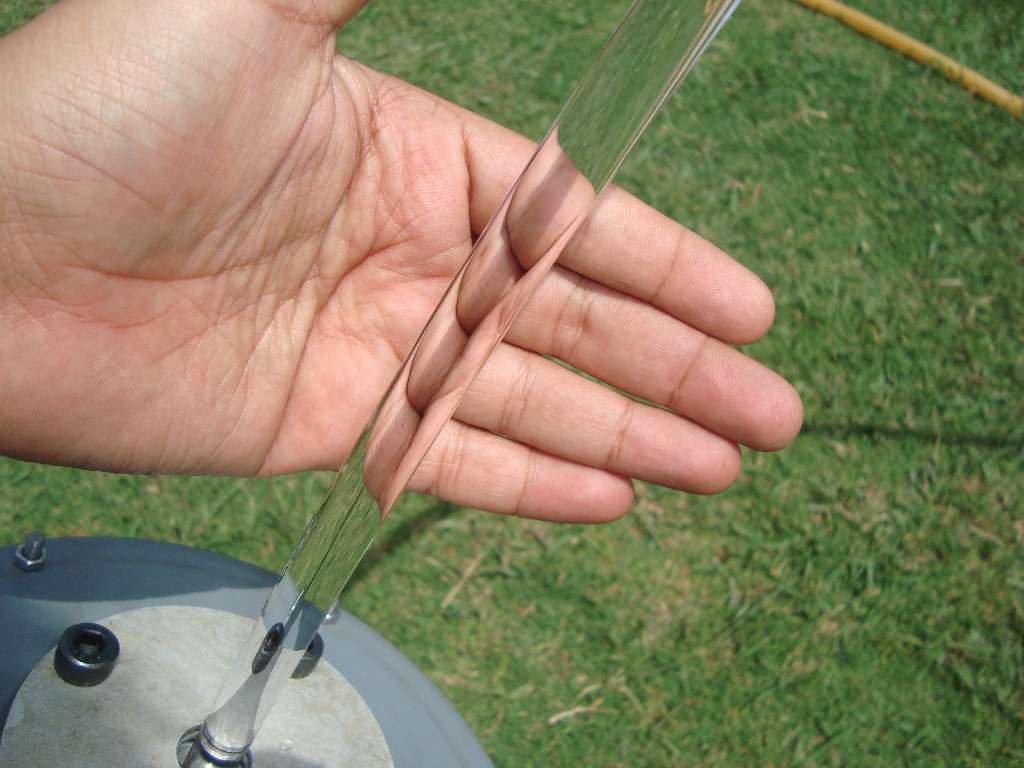
Insert the straw until you can’t fit any more into the jet. Straws are then inserted so that they are parallel with the PVC (perpendicular to the front and back plates. Start with the coarse Brillo at the bottom of the jet, follow this by a few layers of fine Brillo. Place the rubber sheeting and PVC onto the plate. Cut up your Brillo to fit snug within the 4″ piece of PVC, cut a hole in the center so that it can slide over the acrylic rod. Place the plate with the larger end of the acrylic rod facing upward. Small mats of rubber was used to create a gasket between the stainless plates and the PVC pipe.

Once the caulk is cured the jet can be assembled. Allow the silicon to fully cure for about two hours, depending on thickness. Another O-ring, caulk, and retention nut is used on the exterior of the plate to retain the position of the rod on the back plate. Silicone caulk and a rubber O-ring is used on the inside of the drain cache. The acrylic rod is pre-assembled onto the back plate by sliding the rod into the hole cut into the plate with the threaded end point outward toward the back of the jet. Once the epoxy resin is cured a whole-saw is used to cut a 1 7/8″ hole into the back plate of the jet. Once the plumbers putty is in place the rod with attached cache is stood upright and filled with epoxy resin. Plumbers putty is used to seal the gap between the rod and the drain cache. Once the tabs are removed the cache is slid over the rod until approximately 4″ are sticking out of the threaded end. The 3 tabs within the bottom of the drain cache are snipped off with side cutters, if you are good you can use this to properly align the rod within the cache. A standard drain cache, which is used in the basin of most bathroom sinks costs about $3 and is perfect for creating a “through hole” penetration into the bottom plate, making it water tight.
#Laminar flow water cannon install
A buffing compound and cotton rag can then be used to remove the haze from the end of the acrylic rod.Ī simplified install procedure was created using cheap and available parts (other than the acrylic rod). Start at 200 grit and work your way up until you get to 1000 grit. Once the deep saw marks are removed continue smoothing the end using sandpaper. To prep the acrylic rod, cut it square at the end and begin to smooth the end using a file. Some advantages of this include, ruggedness of the rod versus the filaments the ability to make a stand alone lighting rig (waterproofed) that can attach to the back of the rod with a cheap and simple fernco or no-hub pipe fitting and the enlarged surface area allows the light to emit much more proficiently into the stream of water. This design eliminates the need for the fiber optic filaments by using a piece of PMMA core acrylic rod which has the same optical properties as the fiber optic filaments. This is a great idea, however the filaments tend to be very fragile and require you to run them to the location of your lighting emitter and controller. Most lighted laminar jets use fiber optic filaments to carry light through the jet and emit it into the stream of exiting water. The back plate and lighting mechanism is where the real change in design is seen. All openings are thoroughly lathered up with silicone caulk. There is a larger rubber washer that is used as a gasket between the washer and top plate. The stainless washer is attached using 1/8″ stainless pop rivets. This will limit the amount of surface area that contacts the water as it exits the jet, thus creating a more laminar flow. The exit point of the water uses a standard Stainless steel washer that is filed down to a knife edge.
#Laminar flow water cannon crack
Just be careful of the amount of torque applied to the acrylic, as you don’t want to crack it. An after thought, this could be substituted for 1/2″ acrylic if you wanted to see what was going on inside the jet. The purpose of this is to further take the turbulence out of the water by dispersing the flow of water directly into the side of the piece of Brillo rather than force that will create turbulence upward toward the exit tip.įew other laminar jets use the compression plate method for the ends of the jet. Allow this to dry for about 15 minutes to a half hour. The shavings can then be combined with PVC cement creating a 100% solids, particulate bond. Once the hole is drilled a small piece of PVC is filled down and the shavings are collected. Using a 1″ diameter pipe with the PVC 3/4″ garden hose attached.
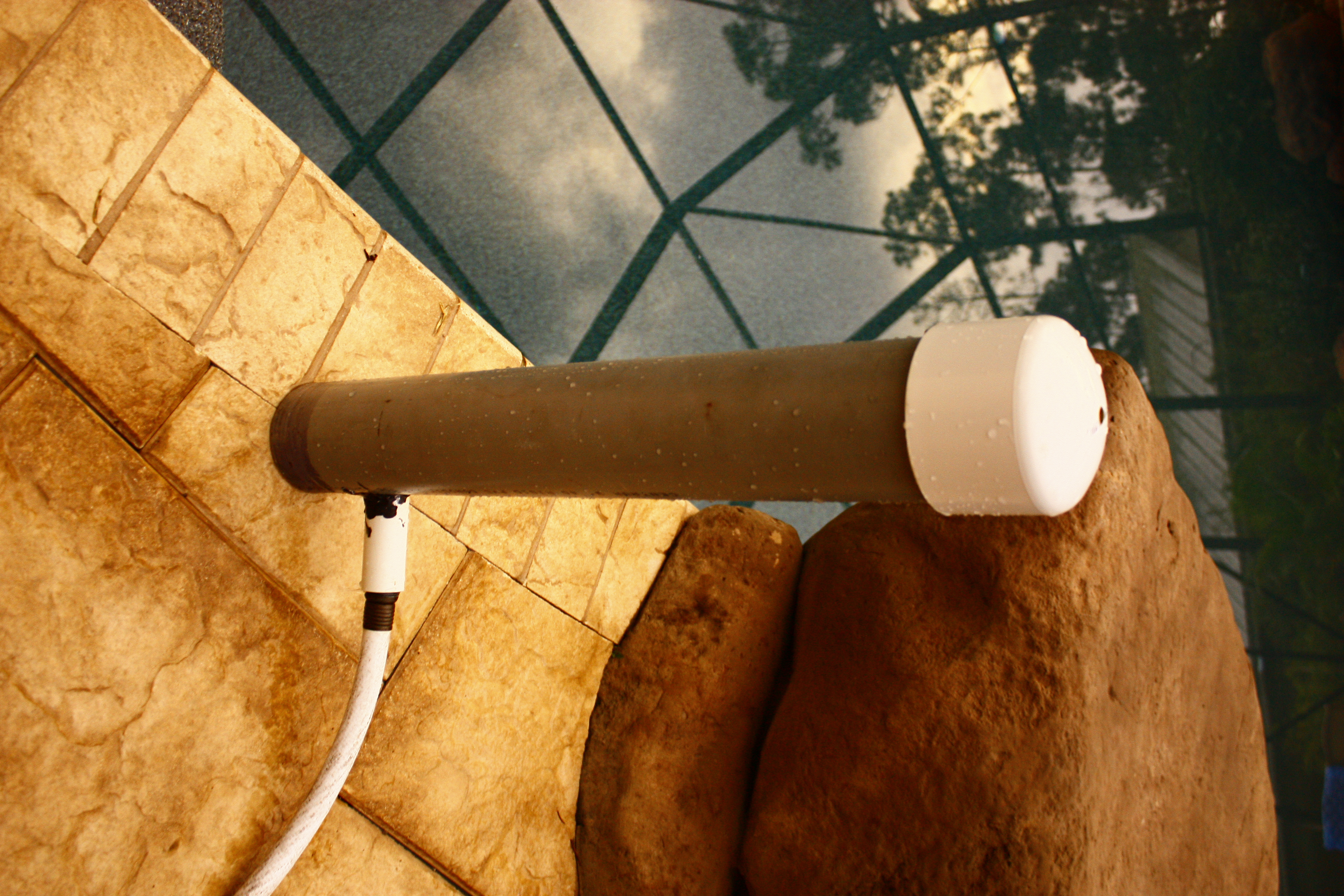
The water inlet is drilled into the side of the pipe, rather than pertruding from the bottom. However there are a few differences between this jet and others you might see. Like most laminar jets this one uses PVC as the enclosure, Brillo pads and straws to create a laminar flow, and a standard 3/4″ garden hose attachment to pump the water into the unit. This write up covers my laminar jet build.
